Пенополистирол отдельными гранулами.
- Багаев Олег
- Сообщения: 529
- Зарегистрирован: 15 авг 2011, 18:22
- Страна, Регион, Область: СССР
- Город: СССР
- Благодарил (а): 0
- Поблагодарили: 21 раз
Пенополистирол отдельными гранулами.
Ребят, проконсультируйте кто в курсе дела. Значит, ситуация такая. Обычно при изготовлении изделий из ППСа всеми силами стараются сделать так, чтобы гранулы слиплись (например, при изготовлении утеплителя или при изготовлении упаковки для бытовой техники). У меня же задача обратная: мне нужно получить вспененные гранулы отдельно друг от друга, то есть не слипшимися. Литературы по ППСу не много, куда бежать не знаю. Проще выяснить на форуме. В связи с этим, имею два вопроса.
1. Есть ли некое готовое оборудование, предназначенное для вспенивания полистирола так, чтобы гранулы не слипались.
2. Если такого оборудования нет, то надо думать об аппаратурном оформлении процесса. Предполагаю, что гранулы можно получить соорудив аппарат кипящего слоя. Опять же, кипящий слой для меня самого - штука сомнительная, так как на мой взгляд, гранулы, чуть расплавившись, сразу начнут слипаться друг с другом. Вспенивание ПСа я никогда не видел, а поэтому совсем не чувствую процессов, происходящих при вспенивании и теряюсь в догадках. Возможно, гранулы и не такие уж и липкие и тогда проще было бы сварганить что-то вроде цилиндра со шнеком, но только шнек не привычный нам, а с большими приваренными лопастями. На цилиндр намотать нагреватель и тогда аппарат получается проще, чем аппарат кипящего слоя.
Кто что думает на этот счёт?
1. Есть ли некое готовое оборудование, предназначенное для вспенивания полистирола так, чтобы гранулы не слипались.
2. Если такого оборудования нет, то надо думать об аппаратурном оформлении процесса. Предполагаю, что гранулы можно получить соорудив аппарат кипящего слоя. Опять же, кипящий слой для меня самого - штука сомнительная, так как на мой взгляд, гранулы, чуть расплавившись, сразу начнут слипаться друг с другом. Вспенивание ПСа я никогда не видел, а поэтому совсем не чувствую процессов, происходящих при вспенивании и теряюсь в догадках. Возможно, гранулы и не такие уж и липкие и тогда проще было бы сварганить что-то вроде цилиндра со шнеком, но только шнек не привычный нам, а с большими приваренными лопастями. На цилиндр намотать нагреватель и тогда аппарат получается проще, чем аппарат кипящего слоя.
Кто что думает на этот счёт?
- Kirilliq
- Сообщения: 2955
- Зарегистрирован: 20 янв 2009, 15:06
- Страна, Регион, Область: Россия
- Город: Москва
- Откуда: из сказки
- Благодарил (а): 201 раз
- Поблагодарили: 983 раза
- Контактная информация:
Re: Пенополистирол отдельными гранулами.
по-моему достаточно пароварки промышленных масштабов. при 100 С, если гранулам будет куда расширяться, они слипаться не должны. Можно еще мешалку присобачить, чтобы процесс равномерно шел.
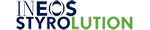
Driving Success.Together
- Багаев Олег
- Сообщения: 529
- Зарегистрирован: 15 авг 2011, 18:22
- Страна, Регион, Область: СССР
- Город: СССР
- Благодарил (а): 0
- Поблагодарили: 21 раз
Re: Пенополистирол отдельными гранулами.
Пароварка - хороший вариант, потому что простой. Вот только почему гранулы не должны слипаться в пароварке? Острым паром, а не воздухом греют, как я понимаю, потому что теплоотдача пара выше, чем у воздуха. А я бы грел дымовыми газами (газовой горелкой, короче говоря). Но люди ведь так не делают, а парятся с паром. Могу предположить, что острый пар используется не столько из-за его теплоотдачи, сколько потому что при трении гранулы немножко дают пыль и рано или поздно в оборудовании у нас накопится пыль выше нижнего концентрационного предела распространения взрыва и тут-то у нас это дело рванёт не хуже снаряда сорокопятки. Или есть другая причина, кроме взрывоопасности и теплоотдачи?
- ПластСтер
- Сообщения: 3068
- Зарегистрирован: 29 окт 2009, 13:15
- Страна, Регион, Область: Россия
- Город: Стерлитамак
- Откуда: Как все
- Благодарил (а): 423 раза
- Поблагодарили: 786 раз
- Контактная информация:
Re: Пенополистирол отдельными гранулами.
Олег, именно пароварка, с мешалкой и свободной зоной для расширения.Kirilliq писал(а):по-моему достаточно пароварки промышленных масштабов. при 100 С, если гранулам будет куда расширяться, они слипаться не должны. Можно еще мешалку присобачить, чтобы процесс равномерно шел.
Сам процесс и заключается в том, чтоб нагреть, и заставить расширяться. Чем меньше количество гранул на объём, тем меньше плотность пенопласта. А водяной пар, как раз и не даст слипаться твоим гранулам. Только потом может появиться следующий вопрос: как сделать гранулы заданного и желательно одинакового размера.
Звать меня, Сергей
-
- Сообщения: 386
- Зарегистрирован: 19 дек 2011, 12:20
- Страна, Регион, Область: Россия
- Город: Москва
- Благодарил (а): 73 раза
- Поблагодарили: 67 раз
Re: Пенополистирол отдельными гранулами.
Нашел ссылку как раз про получение гранул.
Похоже воздухом не стоит греть.
http://ppsdata.ucoz.ru/publ/penopolisti ... a/4-1-0-14
Похоже воздухом не стоит греть.
http://ppsdata.ucoz.ru/publ/penopolisti ... a/4-1-0-14
-
- Сообщения: 385
- Зарегистрирован: 20 июн 2009, 23:08
- Страна, Регион, Область: Ukraine
- Город: ....
- Благодарил (а): 0
- Поблагодарили: 4 раза
Re: Пенополистирол отдельными гранулами.
В технологии EPS сырье - бисерный полистирол, сначала проходит предвспенивание затем созревание и потом формование изделий.
Стандартное оборудование - предвспениватель - представляет собой емкость с мешалкой и подачей водяного пара, которая и производит "шарики".
Конструкцию можно посмотреть на яндексе по ключевому слову - предвспениватель полистирола.
Стандартное оборудование - предвспениватель - представляет собой емкость с мешалкой и подачей водяного пара, которая и производит "шарики".
Конструкцию можно посмотреть на яндексе по ключевому слову - предвспениватель полистирола.
Настоящий Бендеровец
- Багаев Олег
- Сообщения: 529
- Зарегистрирован: 15 авг 2011, 18:22
- Страна, Регион, Область: СССР
- Город: СССР
- Благодарил (а): 0
- Поблагодарили: 21 раз
Re: Пенополистирол отдельными гранулами.
Ребят, спасибо, разобрался. Нужен был толчок какой-то, не знал с чего начать. Всё просто оказалось. Ссылка Ступ-меннеда особенно хороша оказалась. Видно, что писал специалист. У других я никак не мог понять что куда: "...предвспениватель оснащён пневмотранспортом..." мне-то от этого какой толк, оснащён и оснащён. Понятно, что не лопатой из него выгребают. Текст по ссылке на всякий случай копирую на форум, а то он размещён на бесплатном сомнительном сайте, может и пропасть со временем.
_______________________________________________________
Подробное описание процесса производства пенополистирола
ПСВ гранулы являются полистиролом, содержащим легкокипящий компонент (пентан). ПСВ гранулы представляют собой бисерный гранулят, который может поставляться потребителю, как прошедший сепарационное разделение, так и без разделения на фракции. При использовании сеянного гранулята вспененные гранулы полистирола имеют одинаковые размеры, в случае применения, не сеянного гранулята вспененные гранулы полистирола будут иметь значительные расхождения размеров(0,5-12 мм).
Процесс вспенивания ПСВ гранул условно можно разделить на два этапа:
Предварительное вспенивание.
Высушивание (вылеживание) вспененных гранул, для их дальнейшего использования.
Вспенивание.
Активация пентана содержащегося в гранулах ПСВ происходит под воздействием водяного пара. Гранулы ПСВ под действием пара размягчаются и начинают вспениваться, увеличиваясь в объеме. Возможно пятидиситикратное увеличение первоначального объема гранул. Соответственно изменяется и насыпной вес гранул. Например, от 680 гр/л до 14 гр/л.
Для ускорения процесса вспенивания ПСВ гранулы перемещаются в емкости вспенивателя посредством механического активатора-ворошителя. Постоянная циркуляция гранул при воздействии водяного пара позволяет максимально быстро и качественно вспенивать значительные объемы материала. Размер вспененного материала напрямую зависит от температуры и времени воздействия водяного пара, а также скорости вращения и конструкции активатора-ворошителя.
Описание процесса вспенивания гранул ПСВ на установке ПП-40, оснащенной встроенным парогенератором.
Исходное сырье (ПСВ гранулы) из расходного бункера посредством шнекового питателя подается в нижнюю часть вспенивателя. Изменяя количество подаваемого материала (регулятор расходного бункера) регулируется объем вспененных гранул.
Под воздействием водяного пара активируется легкокипящий агент (пентан) содержащийся в ПСВ гранулах. Гранулы увеличиваются в объеме, вытесняются невспененными гранулами, подаваемыми шнековым питателем в нижнюю часть установки, уровень заполнения вспенивателя увеличивается. Вспененные гранулы достигают разгрузочного окна в верхней части емкости вспенивателя и попадают в установку сушки. Меняя высоту шторки разгрузочного окна можно изменять объем вспененных гранул. Чем выше шторка разгрузочного окна и меньше подача сырья шнековым питателем, тем большее время водяной пар воздействует на гранулы ПСВ и тем соответственно больше объем и меньшая плотность вспененных гранул. И, наоборот, при увеличении подачи сырья в установку и нижнем расположении шторки разгрузочного окна увеличивается насыпная плотность готового материала.
Вспенивание ПСВ гранул в установке происходит при постоянном перемешивание материала активатором-ворошителем. Лопасти активатора перемешивают вспененные гранулы, препятствуя слипанию и способствуя равномерному перемещению материала к разгрузочному окну установки, при постоянном воздействии водяного пара.
Сушка материала.
Вспененный полистирол содержит до 10-15% влажности, к тому же внутри гранул создается разряжение вследствие конденсации остатков пентана и водяного пара. Это может привести к деформации (сжатию) вспененных гранул, сжатие гранул резко снижает объем материала и приводит к значительному увеличению насыпной плотности. Поэтому вспененные гранулы ПСВ необходимо просушить, для стабилизации внутреннего давления и упрочнения наружных стенок гранул. Диффузионное проникновение воздуха в ячейки вспененного полистирола придает материалу высокие показатели сопротивления сжатию. Скорость поглощения воздуха вспененными гранулами выше у материала более низкой насыпной плотности.
Сушка-транспортер.
Применение пневмодинамических сушек-транспортеров вспененного полистирола позволяет быстро и эффективно снизить остаточную влажность материала до 6-3% ,одновременно перемещая материал в бункера вылеживания. Бережная транспортировка вспененных гранул в воздушном потоке нагретом, до температуры 35-40°С придает, процессу сушки необходимую динамику и позволяет организовать непрерывную подачу материала на участок вылеживания. Во время прохождения вспененными гранулами установки сушки вместе с потерей остаточной влажности значительно возрастает текучесть материала, что положительно сказывается на наполняемости бункеров вылеживания.
Вылеживание вспененных гранул ПСВ.
Для окончательной стабилизации внутреннего разряжения и достижения показателей остаточной влажности ПСВ гранул на уровне 0,5-1% необходима выдержка материала в бункерах вылеживания. Бункера вылеживания представляют собой легкую сварную конструкцию с закрепленным мешком из воздухопроницаемой ткани. Бункера могут изготавливаться различного объема, ООО «СтройМеханика» предлагает бункера объемом 20 м³. Бункера данного объема удобны в работе и обслуживании, позволяют разместить участок вылеживания практически в любом пригодном для этих целей помещении. Бункера вылеживания соединяются пневмопроводами, объединяющими узел вылежки и позволяющими создать бункерный модуль необходимого объема.
Вспененные гранулы ПСВ находятся в бункере вылеживания около 4-12 часов в зависимости от размера гранул, насыпной плотности и остаточной влажности. Для уменьшения времени выдержки материала в бункере рекомендуется размещать участок вылежки в помещении с пониженной относительной влажностью. Значительного сокращения времени выдержки можно добиться, применив метод перекачивания гранул нагретым воздушным потоком из бункера в бункер. Время выдержки ПСВ гранул в этом случае сокращается до 2-3 часов.
Особенности хранения гранулята ПСВ.
Гранулят ПСВ (ТУ 38.602-22-57-96) поставляется потребителю в основном упакованными в мешках-контейнерах весом 30-50 кг. При закупке материала следует учитывать, что срок хранения ПСВ гранул в мешках не должен превышать шести месяцев с момента изготовления и фасовки. Температура в помещении, где храниться сырье не должна подниматься выше +20°С. Данные ограничения обусловлены снижением содержания в гранулах легкокипящего агента- пентана. Однако вспенивание ПСВ гранулята, для производства полистиролбетона обычно проводиться по одностадийной схеме (при изготовлении листового пенопласта двух стадийная или даже трех стадийная схема) поэтому содержание пентана остается достаточным, для одностадийного вспенивания даже по истечению 12 месяцев с момента производства ПСВ гранулята. Склады хранения должны обеспечивать защиту фасованного гранулята ПСВ от неблагоприятных погодных условий.
Хранение вспененных гранул ПСВ.
Вспененные гранулы ПСВ после выравнивания внутреннего давления имеют достаточно стабильные характеристики, как водопоглощения так и прочности и могут храниться достаточно долго. Однако при вылежке гранул в бункерах необходимо защитить их от воздействия низких температур. При низкой температуре резко замедляется процесс сушки материала, гранулы смерзаются, что отрицательно сказывается на качестве получаемых гранул ПСВ. Температура в производственном помещении не должна опускаться ниже +8°С.
Обязательная вентиляция производственных и складских помещений.
При соединении пентана содержащегося в грануляте ПСВ с воздухом образуется взрывоопасная воздушно-пентановая смесь. Воздушно-пентановая смесь тяжелее воздуха, поэтому необходимо предусмотреть вентиляцию участка вспенивания и вылежки материала на уровне пола. Приток свежего воздуха осуществляется с верху. На крыше производственного здания должны быть установлены вентиляционные люки, обеспечивающие достаточный приток свежего воздуха. На уровне пола рекомендуется установить вытяжной вентилятор.
Над разгрузочным окном вспенивателя и приемной горловиной сушки необходимо установить вытяжные зонты, для предотвращения скапливания пентана (воздушно-пентановой смеси).
Рассмотренная схема производства вспененных гранул ПСВ на основе установки вспенивания ПП-40, позволяет получить до 60 м³ готового материала за восьмичасовую рабочую смену.
Защита вспененных гранул от промерзания.
Необходимо защищать бункеры для вылежки гранул от воздействия крайне низких температур, поскольку это может привести к замерзанию материала, и следственно к потере им своих качеств. Помимо этого не забывайте что едва вспененные гранулы легко теряют объём при контакте с холодным воздухом. Температура ни в коем случае не должна опускаться ниже 10°С.
Использование отходов.
Отходы представляют собой ценное сырье, но в силу своих габаритных размеров не могут использоваться для этой цели. Поэтому предусматривается, либо измельчение отходов с последующей транспортировкой их в бункера вылежки гранул , либо повторное запекание в процессе формирования блоков в соотношении от 10 до 20%.
Производство блоков полистирола.
Формовочный агрегат представляет собой стальную конструкцию прямоугольной формы с двойными стенками, внутренние стенки, перфорированные по всей поверхности для обеспечения возможности поступления пара.
Технологический цикл функционирования формовочного агрегата протекает следующим образом:
Закрывание дверей.
Закрывание затворов.
Разогрев камеры. На этой стадии подается пар для разогрева камеры (эту операцию рекомендуется производить в начале работы каждой смены ).
Сброс конденсата. Сброс конденсата производится путем открывания спускного клапана и последующим сливом конденсата.
Загрузка материала. Открывается верхний борт и в формовочный агрегат загружается порциями материал.
Герметичное закрывание формовочного агрегата.
Первая подача пара. Пар подается в камеры, при этом линия слива конденсата должна быть обязательно открыта. Это позволяет пару пройти через всю толщу материала и одновременно со сливом конденсата произвести формовку. Содержание линии слива конденсата в открытом состоянии позволяет осуществить стабилизацию давления на значении, близком к атмосферному, что в свою очередь обеспечивает оптимальное распределение пара по всему объему материала.
Перекрытие линии слива конденсата.
Подача пара. Снова подается пар и агрегат выводится на рабочее давление (ориентировочно 0,5 кг/см²), по достижении заданной величины давления, начинается отсчет времени, предусмотренного на стабилизацию материала.
Стабилизация материала.
Открывание линии слива конденсата. Линия слива конденсата открывается, и конденсат пара сливается. При этом внутренне давление внутри камеры приводится в соответствии с давлением снаружи ее. Время открывания линии сброса, используется также как время охлаждения блока.
Открывание дверей.
Извлечение блока. Блок извлекается из агрегата, взвешивается и удаляется из рабочей зоны. По истечению кратковременного периода охлаждения, блоки укладываются в склад на хранения на период, длительность которого зависит от сферы применения будущей продукции, которая будет изготавливаться из этого материала.
Резка блока на листы.
По завершению вызревания блок подлежит резке на листы различной толщины. Для проведения этих операций используется установка для резки. С помощью разогретых струн диаметром 0,5 мм. Выполняется резка блока по высоте от 0 до 400 мм. Присутствие незначительного количества дыма вызвано неверной установкой скорости реза и температуры струны. Скорость резки установки определяется плотностью, шириной реза и диаметром струны, которые в этом случае составляют 0,5 мм. В непосредственной близости от установки рекомендуется постоянно держать в наличии огнетушители с двуокисью углерода.
Складирование плит пенополистирола.
Складирование плит пенополистирола должно осуществляться согласно п. 5.7 ГОСТ 15588-86. При формировании пакетов должны соблюдаться требования ГОСТ 21929-76 и ГОСТ 24510-80.
_______________________________________________________
Подробное описание процесса производства пенополистирола
ПСВ гранулы являются полистиролом, содержащим легкокипящий компонент (пентан). ПСВ гранулы представляют собой бисерный гранулят, который может поставляться потребителю, как прошедший сепарационное разделение, так и без разделения на фракции. При использовании сеянного гранулята вспененные гранулы полистирола имеют одинаковые размеры, в случае применения, не сеянного гранулята вспененные гранулы полистирола будут иметь значительные расхождения размеров(0,5-12 мм).
Процесс вспенивания ПСВ гранул условно можно разделить на два этапа:
Предварительное вспенивание.
Высушивание (вылеживание) вспененных гранул, для их дальнейшего использования.
Вспенивание.
Активация пентана содержащегося в гранулах ПСВ происходит под воздействием водяного пара. Гранулы ПСВ под действием пара размягчаются и начинают вспениваться, увеличиваясь в объеме. Возможно пятидиситикратное увеличение первоначального объема гранул. Соответственно изменяется и насыпной вес гранул. Например, от 680 гр/л до 14 гр/л.
Для ускорения процесса вспенивания ПСВ гранулы перемещаются в емкости вспенивателя посредством механического активатора-ворошителя. Постоянная циркуляция гранул при воздействии водяного пара позволяет максимально быстро и качественно вспенивать значительные объемы материала. Размер вспененного материала напрямую зависит от температуры и времени воздействия водяного пара, а также скорости вращения и конструкции активатора-ворошителя.
Описание процесса вспенивания гранул ПСВ на установке ПП-40, оснащенной встроенным парогенератором.
Исходное сырье (ПСВ гранулы) из расходного бункера посредством шнекового питателя подается в нижнюю часть вспенивателя. Изменяя количество подаваемого материала (регулятор расходного бункера) регулируется объем вспененных гранул.
Под воздействием водяного пара активируется легкокипящий агент (пентан) содержащийся в ПСВ гранулах. Гранулы увеличиваются в объеме, вытесняются невспененными гранулами, подаваемыми шнековым питателем в нижнюю часть установки, уровень заполнения вспенивателя увеличивается. Вспененные гранулы достигают разгрузочного окна в верхней части емкости вспенивателя и попадают в установку сушки. Меняя высоту шторки разгрузочного окна можно изменять объем вспененных гранул. Чем выше шторка разгрузочного окна и меньше подача сырья шнековым питателем, тем большее время водяной пар воздействует на гранулы ПСВ и тем соответственно больше объем и меньшая плотность вспененных гранул. И, наоборот, при увеличении подачи сырья в установку и нижнем расположении шторки разгрузочного окна увеличивается насыпная плотность готового материала.
Вспенивание ПСВ гранул в установке происходит при постоянном перемешивание материала активатором-ворошителем. Лопасти активатора перемешивают вспененные гранулы, препятствуя слипанию и способствуя равномерному перемещению материала к разгрузочному окну установки, при постоянном воздействии водяного пара.
Сушка материала.
Вспененный полистирол содержит до 10-15% влажности, к тому же внутри гранул создается разряжение вследствие конденсации остатков пентана и водяного пара. Это может привести к деформации (сжатию) вспененных гранул, сжатие гранул резко снижает объем материала и приводит к значительному увеличению насыпной плотности. Поэтому вспененные гранулы ПСВ необходимо просушить, для стабилизации внутреннего давления и упрочнения наружных стенок гранул. Диффузионное проникновение воздуха в ячейки вспененного полистирола придает материалу высокие показатели сопротивления сжатию. Скорость поглощения воздуха вспененными гранулами выше у материала более низкой насыпной плотности.
Сушка-транспортер.
Применение пневмодинамических сушек-транспортеров вспененного полистирола позволяет быстро и эффективно снизить остаточную влажность материала до 6-3% ,одновременно перемещая материал в бункера вылеживания. Бережная транспортировка вспененных гранул в воздушном потоке нагретом, до температуры 35-40°С придает, процессу сушки необходимую динамику и позволяет организовать непрерывную подачу материала на участок вылеживания. Во время прохождения вспененными гранулами установки сушки вместе с потерей остаточной влажности значительно возрастает текучесть материала, что положительно сказывается на наполняемости бункеров вылеживания.
Вылеживание вспененных гранул ПСВ.
Для окончательной стабилизации внутреннего разряжения и достижения показателей остаточной влажности ПСВ гранул на уровне 0,5-1% необходима выдержка материала в бункерах вылеживания. Бункера вылеживания представляют собой легкую сварную конструкцию с закрепленным мешком из воздухопроницаемой ткани. Бункера могут изготавливаться различного объема, ООО «СтройМеханика» предлагает бункера объемом 20 м³. Бункера данного объема удобны в работе и обслуживании, позволяют разместить участок вылеживания практически в любом пригодном для этих целей помещении. Бункера вылеживания соединяются пневмопроводами, объединяющими узел вылежки и позволяющими создать бункерный модуль необходимого объема.
Вспененные гранулы ПСВ находятся в бункере вылеживания около 4-12 часов в зависимости от размера гранул, насыпной плотности и остаточной влажности. Для уменьшения времени выдержки материала в бункере рекомендуется размещать участок вылежки в помещении с пониженной относительной влажностью. Значительного сокращения времени выдержки можно добиться, применив метод перекачивания гранул нагретым воздушным потоком из бункера в бункер. Время выдержки ПСВ гранул в этом случае сокращается до 2-3 часов.
Особенности хранения гранулята ПСВ.
Гранулят ПСВ (ТУ 38.602-22-57-96) поставляется потребителю в основном упакованными в мешках-контейнерах весом 30-50 кг. При закупке материала следует учитывать, что срок хранения ПСВ гранул в мешках не должен превышать шести месяцев с момента изготовления и фасовки. Температура в помещении, где храниться сырье не должна подниматься выше +20°С. Данные ограничения обусловлены снижением содержания в гранулах легкокипящего агента- пентана. Однако вспенивание ПСВ гранулята, для производства полистиролбетона обычно проводиться по одностадийной схеме (при изготовлении листового пенопласта двух стадийная или даже трех стадийная схема) поэтому содержание пентана остается достаточным, для одностадийного вспенивания даже по истечению 12 месяцев с момента производства ПСВ гранулята. Склады хранения должны обеспечивать защиту фасованного гранулята ПСВ от неблагоприятных погодных условий.
Хранение вспененных гранул ПСВ.
Вспененные гранулы ПСВ после выравнивания внутреннего давления имеют достаточно стабильные характеристики, как водопоглощения так и прочности и могут храниться достаточно долго. Однако при вылежке гранул в бункерах необходимо защитить их от воздействия низких температур. При низкой температуре резко замедляется процесс сушки материала, гранулы смерзаются, что отрицательно сказывается на качестве получаемых гранул ПСВ. Температура в производственном помещении не должна опускаться ниже +8°С.
Обязательная вентиляция производственных и складских помещений.
При соединении пентана содержащегося в грануляте ПСВ с воздухом образуется взрывоопасная воздушно-пентановая смесь. Воздушно-пентановая смесь тяжелее воздуха, поэтому необходимо предусмотреть вентиляцию участка вспенивания и вылежки материала на уровне пола. Приток свежего воздуха осуществляется с верху. На крыше производственного здания должны быть установлены вентиляционные люки, обеспечивающие достаточный приток свежего воздуха. На уровне пола рекомендуется установить вытяжной вентилятор.
Над разгрузочным окном вспенивателя и приемной горловиной сушки необходимо установить вытяжные зонты, для предотвращения скапливания пентана (воздушно-пентановой смеси).
Рассмотренная схема производства вспененных гранул ПСВ на основе установки вспенивания ПП-40, позволяет получить до 60 м³ готового материала за восьмичасовую рабочую смену.
Защита вспененных гранул от промерзания.
Необходимо защищать бункеры для вылежки гранул от воздействия крайне низких температур, поскольку это может привести к замерзанию материала, и следственно к потере им своих качеств. Помимо этого не забывайте что едва вспененные гранулы легко теряют объём при контакте с холодным воздухом. Температура ни в коем случае не должна опускаться ниже 10°С.
Использование отходов.
Отходы представляют собой ценное сырье, но в силу своих габаритных размеров не могут использоваться для этой цели. Поэтому предусматривается, либо измельчение отходов с последующей транспортировкой их в бункера вылежки гранул , либо повторное запекание в процессе формирования блоков в соотношении от 10 до 20%.
Производство блоков полистирола.
Формовочный агрегат представляет собой стальную конструкцию прямоугольной формы с двойными стенками, внутренние стенки, перфорированные по всей поверхности для обеспечения возможности поступления пара.
Технологический цикл функционирования формовочного агрегата протекает следующим образом:
Закрывание дверей.
Закрывание затворов.
Разогрев камеры. На этой стадии подается пар для разогрева камеры (эту операцию рекомендуется производить в начале работы каждой смены ).
Сброс конденсата. Сброс конденсата производится путем открывания спускного клапана и последующим сливом конденсата.
Загрузка материала. Открывается верхний борт и в формовочный агрегат загружается порциями материал.
Герметичное закрывание формовочного агрегата.
Первая подача пара. Пар подается в камеры, при этом линия слива конденсата должна быть обязательно открыта. Это позволяет пару пройти через всю толщу материала и одновременно со сливом конденсата произвести формовку. Содержание линии слива конденсата в открытом состоянии позволяет осуществить стабилизацию давления на значении, близком к атмосферному, что в свою очередь обеспечивает оптимальное распределение пара по всему объему материала.
Перекрытие линии слива конденсата.
Подача пара. Снова подается пар и агрегат выводится на рабочее давление (ориентировочно 0,5 кг/см²), по достижении заданной величины давления, начинается отсчет времени, предусмотренного на стабилизацию материала.
Стабилизация материала.
Открывание линии слива конденсата. Линия слива конденсата открывается, и конденсат пара сливается. При этом внутренне давление внутри камеры приводится в соответствии с давлением снаружи ее. Время открывания линии сброса, используется также как время охлаждения блока.
Открывание дверей.
Извлечение блока. Блок извлекается из агрегата, взвешивается и удаляется из рабочей зоны. По истечению кратковременного периода охлаждения, блоки укладываются в склад на хранения на период, длительность которого зависит от сферы применения будущей продукции, которая будет изготавливаться из этого материала.
Резка блока на листы.
По завершению вызревания блок подлежит резке на листы различной толщины. Для проведения этих операций используется установка для резки. С помощью разогретых струн диаметром 0,5 мм. Выполняется резка блока по высоте от 0 до 400 мм. Присутствие незначительного количества дыма вызвано неверной установкой скорости реза и температуры струны. Скорость резки установки определяется плотностью, шириной реза и диаметром струны, которые в этом случае составляют 0,5 мм. В непосредственной близости от установки рекомендуется постоянно держать в наличии огнетушители с двуокисью углерода.
Складирование плит пенополистирола.
Складирование плит пенополистирола должно осуществляться согласно п. 5.7 ГОСТ 15588-86. При формировании пакетов должны соблюдаться требования ГОСТ 21929-76 и ГОСТ 24510-80.
Кто сейчас на конференции
Сейчас этот форум просматривают: нет зарегистрированных пользователей и 36 гостей